Have you ever sold an inventory item just to be told by the warehouse that the item is no longer in stock? Do you have unreliable financials due to large inventory count fluctuations consistently month after month? Does your inventory disappear, but sales aren’t reflected? If you answered “yes” to any of these questions, I suggest reading on for guidance in order to get your inventory count process running smoothly so that your books reflect accurate figures.
Why Do You Perform a Physical Inventory Count?
Performing an inventory count is crucial to ensure accurate inventory records at the end of a reporting period. Having current inventory records ensures you know the correct inventory on hand, don’t accidentally oversell an item, and provides for better forecasts and planning to make informed financial decisions. I’ve often seen companies rely on their inventory management system to provide an actual count of stock on hand, but this is only sometimes the case, as there could be theft, spoilage, or errors in shipping. The physical counts are a way to verify that the inventory system, financials, and actual physical stock agree.
Another reason it’s essential to take a physical inventory is that the quantity of your inventory can impact the value of your inventory on the balance sheet. Suppose there are variances in quantity reported on the books versus the quantity counted. In that case, the books must be adjusted to reflect the actual inventory value on hand accurately.
What is a Physical Inventory Count?
A physical inventory count is a structured approach to physically counting the number of items in the company’s inventory and comparing that number to the number in the inventory management system and financials. This is usually done at the end of a month, quarter, or year to coincide with the end of a reporting period, but it can also be done periodically. Four inventory count methods can be used based on a company’s resources, and the best method depends on your business type and goals.
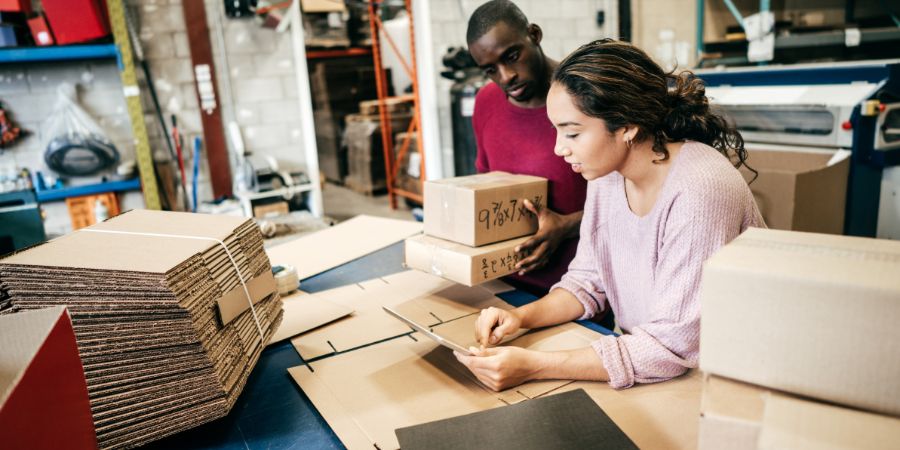
Types of Physical Inventory Counts
In preparing for an inventory count, you would select either doing a cycle count or a physical count and counting the items manually or electronically. There are pros and cons to each, which I will mention below.
- Cycle Count– The process of counting random portions or rotating sections of inventory at any given time. An example of this would be to count one inventory SKU per day.
- Pros- It can help save time and resources by allowing you to complete the count in manageable sections and avoid operational closures.
- Cons-Not as accurate as a full count
- Full Physical Count– Using current employees and/or bringing in temporary staff to count all stock simultaneously.
- Pros-Provides the most accurate inventory records for annual financials
- Cons-This method may require operational shutdown and is labor and time intensive.
- Manual Counting- Method of counting where you would record the results using paper and pen. Once the count is completed, all numbers are compiled and reviewed for accuracy.
- Pros- Inexpensive cost of materials
- Cons- High rate of manual errors
- Electronic Counting- Method of counting where you would use scanners, barcodes, or mobile devices to scan the items into an inventory management system.
- Pros-Greatly reduces manual errors, and digital records make it much easier to track inventory levels.
- Cons- The company would need to invest in specialized technology to get the system in place
Steps in Performing an Inventory Count
Pre-Count Steps (Plan & Prepare)
- Schedule the count- There are many items to prepare for before the count can start. Scheduling a reasonable date is crucial to ensure you have committed manpower available to count on that date. All inventory in all locations should be counted simultaneously to give a clear picture of the inventory on hand. All storage locations should be informed of the count date and procedures. Also, if you need to close during business hours, customers or appropriate parties should be notified of the closure well in advance.
- Assign your counters – It’s ideal to have a two-person team to count the inventory- one to count and one to record. A level of experience with counting should come into play when assigning a count team, as you would want to avoid pairing two inexperienced counters with each other. Distribute to the counters the documented count procedures from start to finish so that the counters can be familiar with the process well in advance- you might even want to hold a training to go over the procedure. Emphasize the importance of counting accurately and efficiently. Creating a warehouse or floor map of the space where inventory is held would be beneficial to assign certain sections of the map to count teams.
- Order count tags- If a manual count is being completed, a sufficient number of sequentially numbered two-part count tags should be on hand or ordered
- Complete Data Entry & Create clear cut-offs- All data entry of inventory transactions needs to be performed before the count; then, all warehouse activities should be frozen until after the count to have a clear cut-off. Depending on the inventory management software, there are times when the system shows that inventory is depleted when the inventory has yet to leave the facility (sold, not yet shipped). These items should not be included in the count since the system already shows them as depleted, so the items not to be counted should be blocked off from counted inventory.
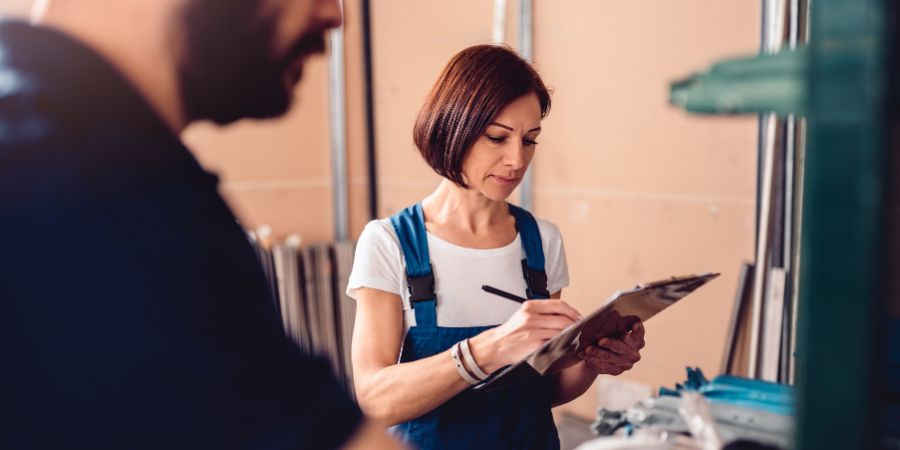
Count Steps (Execution)
- Instruct count teams- Give a refresher of the count training to the count teams again so that they are reminded of the procedure
- Assign count areas- Assign a specific section of the floor map to each count team. The person in charge of the count should have a master listing of which count teams are assigned to each area.
- Issue Count Tags- A sequential number of count tags will be given to each count team, who will be responsible for turning in all tags, whether they are used or not. The person in charge of the count should have a master listing of the numbered tags issued to each count team. Maintaining control over count tags ensures that lost tags will be investigated promptly.
- Count inventory- Once count teams have the count tags and assigned count area, they can start the count. One person will count, and the other will record the inventory specifics on the count tag (SKU, item description, location, quantity, and unit of measure), affixing one copy of the count tag to the inventory, which shows that inventory is counted, and retains the other portion of the count tag to turn in to the person in charge of the count. If time permits, have the person recording the data also recount the inventory to ensure it agrees to the tag details.
Post-Count Steps (Verify & Record)
- Verify Tags – Ensure that all issued sequential count tags are returned to the person in charge of the count upon completion. Also, walk around to ensure count tags are affixed to all inventory and no inventory on the floor is missing a tag.
- Enter Tag Information- Enter the data from the count tags into a spreadsheet, and pull in the system count (book) numbers to compare.
- Investigate Discrepancies- if there are significant discrepancies, consider recounting that SKU or area to confirm the correct count figures.
- True up book figures to count- once everything is counted, verified, and discrepancies looked into, it’s time to true up your book quantities to count within the system of record.
Completing an accurate physical inventory count can take a substantial amount of time and effort, which is one of the reasons why organizations limit the number of counts they perform each year. Still, it can have huge benefits and helps you see the accurate picture. With thoughtful planning, inventory season can be something your team looks forward to. With successful inventory counts, you can take corrective and preventative action to protect one of your most valuable assets — your stock.
Frequently Asked Questions
1. Why is conducting a physical inventory count important?
Conducting a physical inventory count ensures you have accurate, up-to-date records of stock levels, which is essential for avoiding discrepancies between your inventory management software and the actual items on hand. Regular inventory checks help prevent overselling products that are no longer available and highlight theft, spoilage, or unrecorded returns. Without these counts, you could be making critical financial decisions based on inaccurate data, which can severely impact your business’s bottom line.
2. How often should businesses perform physical inventory counts?
The frequency of physical inventory counts depends on the size and complexity of your operations. Some businesses conduct counts monthly or quarterly, while others rely on an annual count. Cycle counting—a method of counting smaller portions of inventory at regular intervals—offers a time-efficient alternative that helps maintain accuracy without the need for full operational shutdowns. Ideally, businesses should choose a schedule that aligns with their reporting periods and minimizes disruption.
3. What’s the difference between cycle counting and full physical counts?
Cycle counting involves regularly checking a portion of your inventory in smaller, manageable segments, making it less disruptive to daily operations. Full physical counts, on the other hand, involve counting all inventory at once, typically at the end of a fiscal year. While cycle counting is quicker and can be done more frequently, a full count provides the most accurate inventory data. Both methods have their pros and cons depending on your business size and goals.
4. What causes discrepancies between physical stock and inventory records?
Discrepancies can arise from theft, spoilage, miscounted items, or administrative errors in your inventory management software. For instance, a shipment may be recorded in the system but never physically received, or damaged goods might be discarded without proper documentation. Another common issue is human error during manual counts. Implementing a structured inventory count process with electronic scanners can help mitigate these issues and improve accuracy.
5. What are the best practices for ensuring an accurate physical inventory count?
To ensure accuracy, start by scheduling your count at a time that minimizes disruptions. Create clear cut-offs for transactions to avoid confusion, and assign experienced team members to counting roles. Using count tags and electronic devices can help maintain consistency, and conducting random spot checks can further verify the accuracy of the counts. Training your staff and utilizing inventory management software that syncs with your physical counts will also help streamline the process.
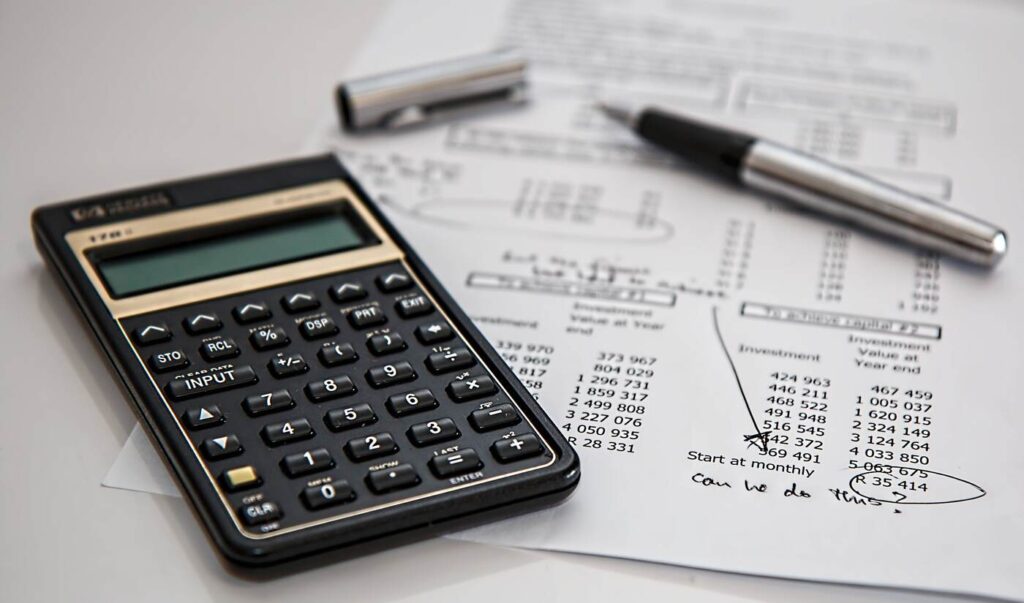
6. How do inventory count discrepancies affect financial statements?
Inventory discrepancies directly impact your financials by affecting both the balance sheet and the income statement. Overstated inventory can lead to inflated asset values, while understated inventory could result in inaccurate cost of goods sold (COGS) figures, ultimately skewing profit margins. Adjusting your books to reflect the actual physical inventory ensures that financial reports provide a true picture of your business’s health, which is crucial for decision-making and tax reporting.
7. What tools can improve inventory count accuracy?
Investing in inventory management software that integrates with barcode scanners or RFID tags can drastically reduce manual errors. These systems automate much of the counting process, allowing for real-time updates and fewer mistakes. Additionally, using cloud-based systems enables remote access and better tracking, while some software can even alert you to potential stock issues before they become problematic. The right tools can turn an otherwise tedious process into a streamlined, accurate system.
8. Can manual counting be reliable, or should businesses go fully digital?
While manual counting can still be reliable for small businesses with low SKU counts, the risk of human error increases as your inventory grows. Going digital with scanners or inventory management software reduces these risks and increases speed. However, many businesses find a hybrid approach—manual counting combined with electronic verification—works best for their operations. It’s all about finding the right balance for your needs and budget.
9. How do I handle inventory that’s been sold but hasn’t shipped yet during a count?
Inventory that has been sold but not yet shipped should be excluded from the physical count, as it’s technically still in stock but no longer part of your available inventory. Using count tags and segregating such items from the rest of your stock can help avoid confusion. Proper cut-off procedures ensure your system reflects accurate figures for the reporting period, preventing discrepancies between the actual inventory and what’s recorded in your books.
10. What are the most common challenges during physical inventory counts?
Some common challenges include operational downtime, miscounts, and managing discrepancies between recorded and physical stock. Another issue can be staffing—having inexperienced workers count inventory can lead to mistakes that snowball into financial reporting errors. Scheduling, training, and implementing a well-organized process, including the use of technology like scanners and management software, can help mitigate these challenges.
Let Protea Financial Help You Understand Inventory Management
Inventory management is essential to running a successful business, but the task can take time and effort. Whether you choose to do it yourself or outsource the work to a professional, having accurate records will help you make better decisions and maximize profits. Contact Protea Financial today to learn more about inventory management services offered to help get your processes around accounting for inventory on track.
Contact Protea Financial today for help with inventory management, counting inventory, or any other bookkeeping task you may have!